Quick Start Guide
Running a risk analysis
Assessing galvanic corrosion risk between material couples is quick and easy with Corrosion Djinn.
Go to the https://corrosiondjinn.com website. You can then create groups of material pairs for examination. So first you enter the environment, Figure 1, and then you create your first group by making your choices for the individual materials in the material pairs.
In Djinn, materials are defined by using four descriptors, so in this example if we want to examine the interface between an Aluminum alloy and a Stainless Steel we would make our choices as follows
- Substrate - Figure 2
- Designation - Figure 3
- Coating - Figure 4
- Treatment - Figure 5
- Choice of second material - Figure 6
- Results - Figure 7
- Adding further groups
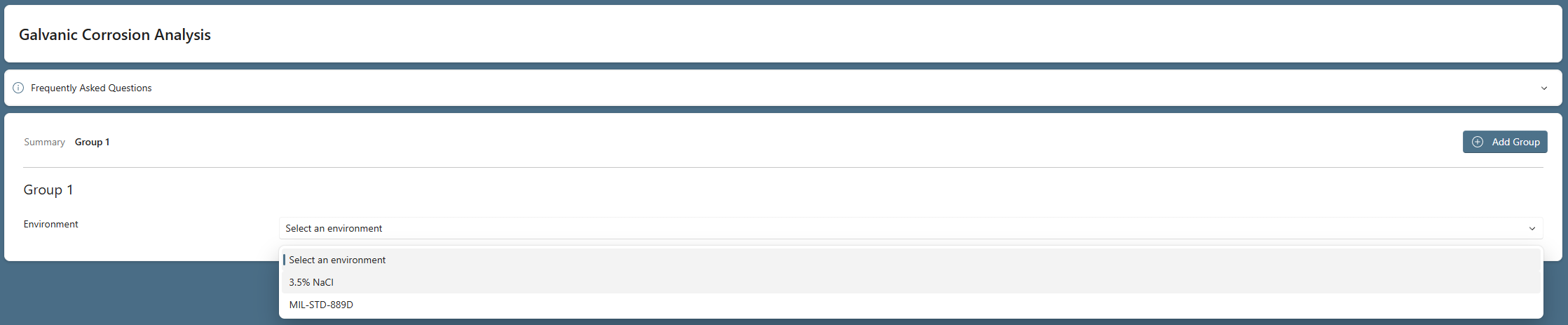
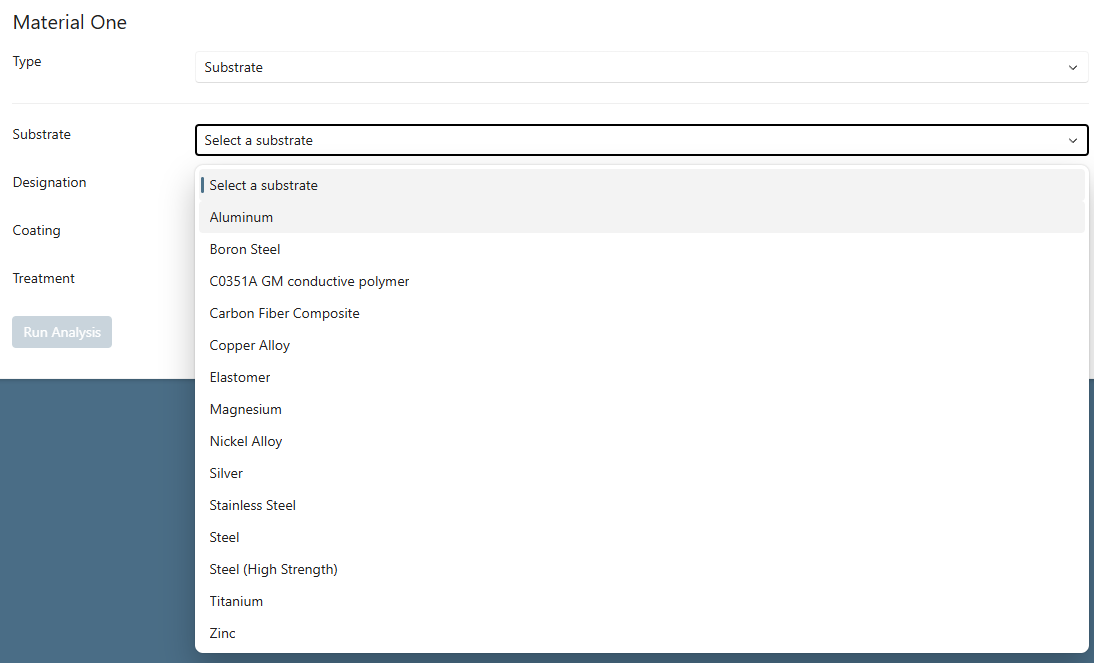
By substrate we mean the underlying base material, which could be an element or alloy.
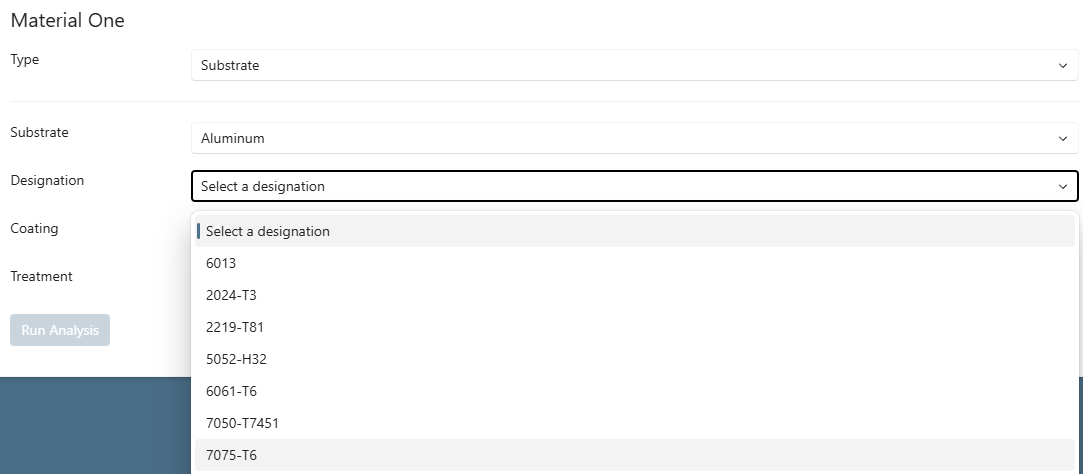
If an alloy is being considered, for example, then designation allows the user to be a little more specific, permitting the user to specify a particular alloy series or heat treatment.
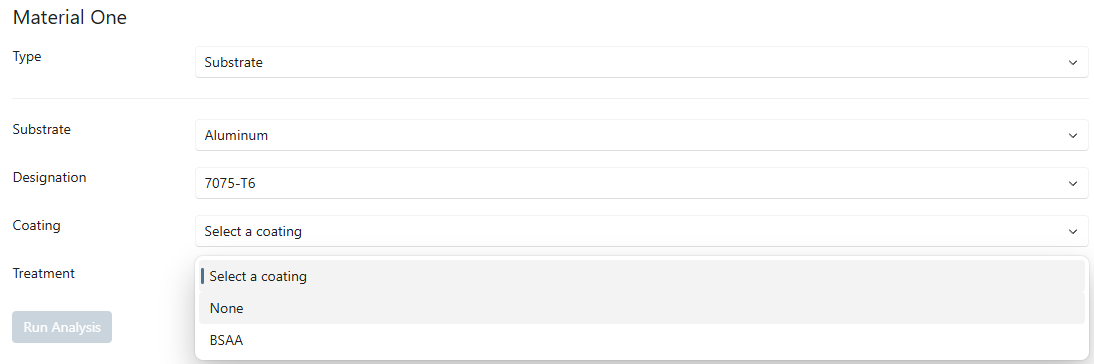
The user also has the opportunity to specify a coating, which, in the case of Figure 4, would allow the user to specify an anodized aluminum alloy.
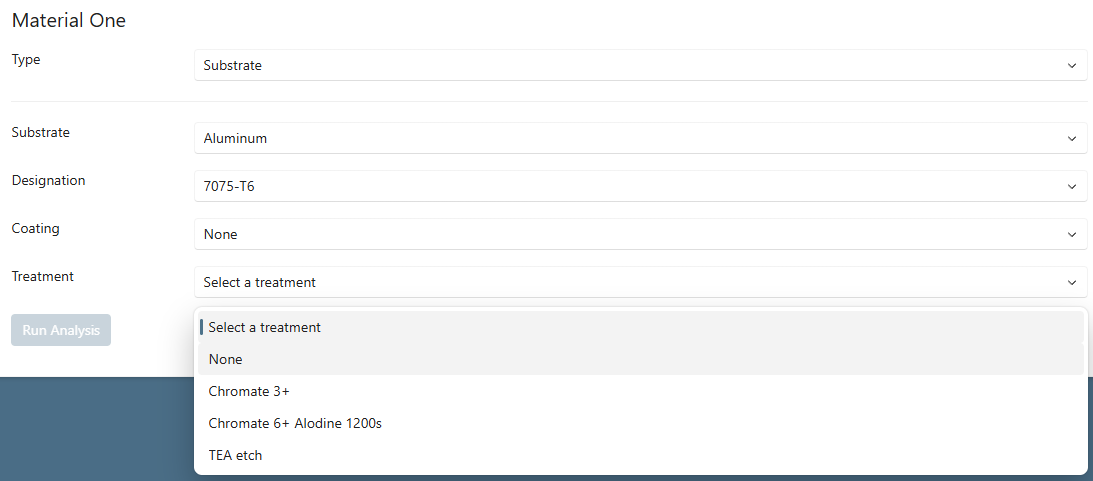
Finally, the user also has an opportunity to specify a treatment. For example, in the case of an anodized aluminum alloy, treatment allows the user to specify the final “finish” to the anodized layer such as chromate or hot water seal etc. The user then makes selections for the Second Material of the couple. Figure 6 shows selections for the second material Stainless Steel 15-5 PH which is coupled to bare Aluminum alloy 7075-T6. When satisfied with the materials selections for the first group the user then clicks Run Analysis.
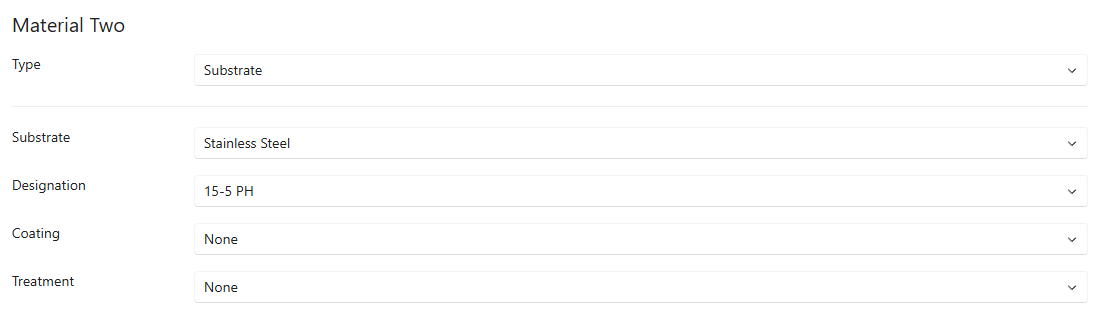
The user now chooses the option to Run Analysis, which provides a plot of the material polarization curves and a summary table of the material compatibility results for this particular couple, see Figure 7. Djinn annotates each material in the couple as anode and cathode according to their relative OCPs (Open Circuit Potentials), anodic materials having a more negative OCP.
The Djinn electrochemical database also contains material self-corrosion rates and these can be seen for each material, the bare Al-7075 T6 having a self-corrosion rate of 19.1 microns per year compared to the stainless steel 15-5 PH which only has a self-corrosion rate of 1.08 micron/year which is essentially negligible. However, there is a galvanic impact resulting from these particular materials being adjacent to one another, this is reflected in the galvanic corrosion rate, of 128 microns/year shown in the summary portion of the table. The inference is that although the aluminum alloy has a self-corrosion rate of 19.1 microns/year, this is accelerated when in galvanic contact with the 15-5 PH stainless steel to 128 microns/year. This is captured in the reported Galvanic Acceleration Factor of 6.7. A summary report can be printed to file using the ‘print’ button.
Adding more groups
More material pairs (groups) can be added for comparison by clicking the Copy button. This copies the current group and gives it the next sequential Group #. After making any changes, clicking the Run Analysis button saves it to the next group. Any number of additional groups can be added in this way.
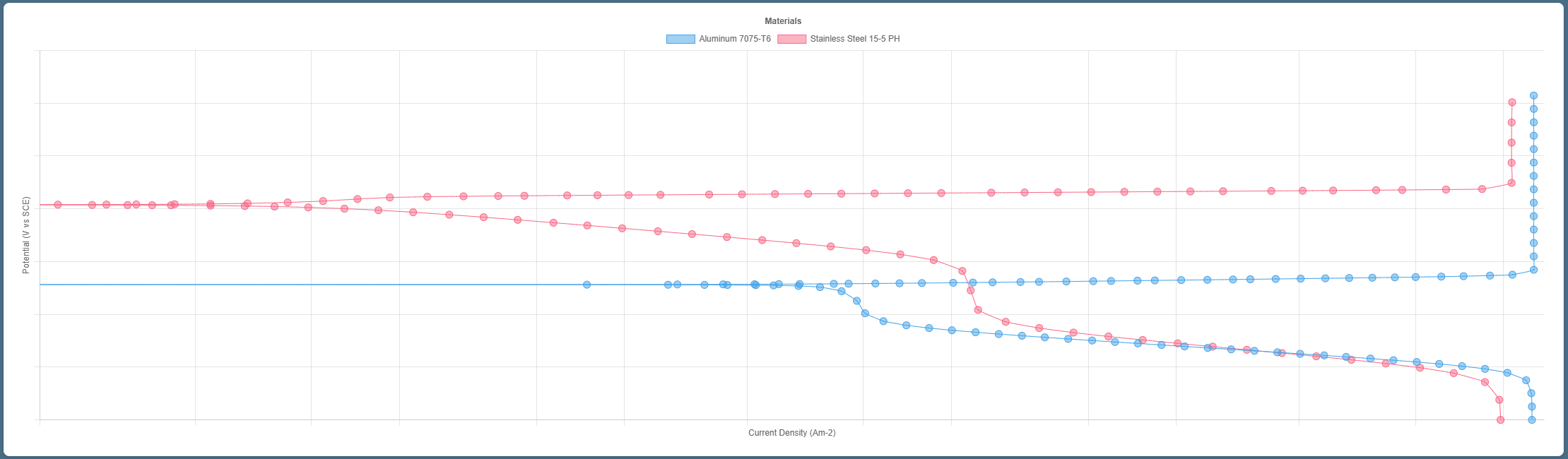
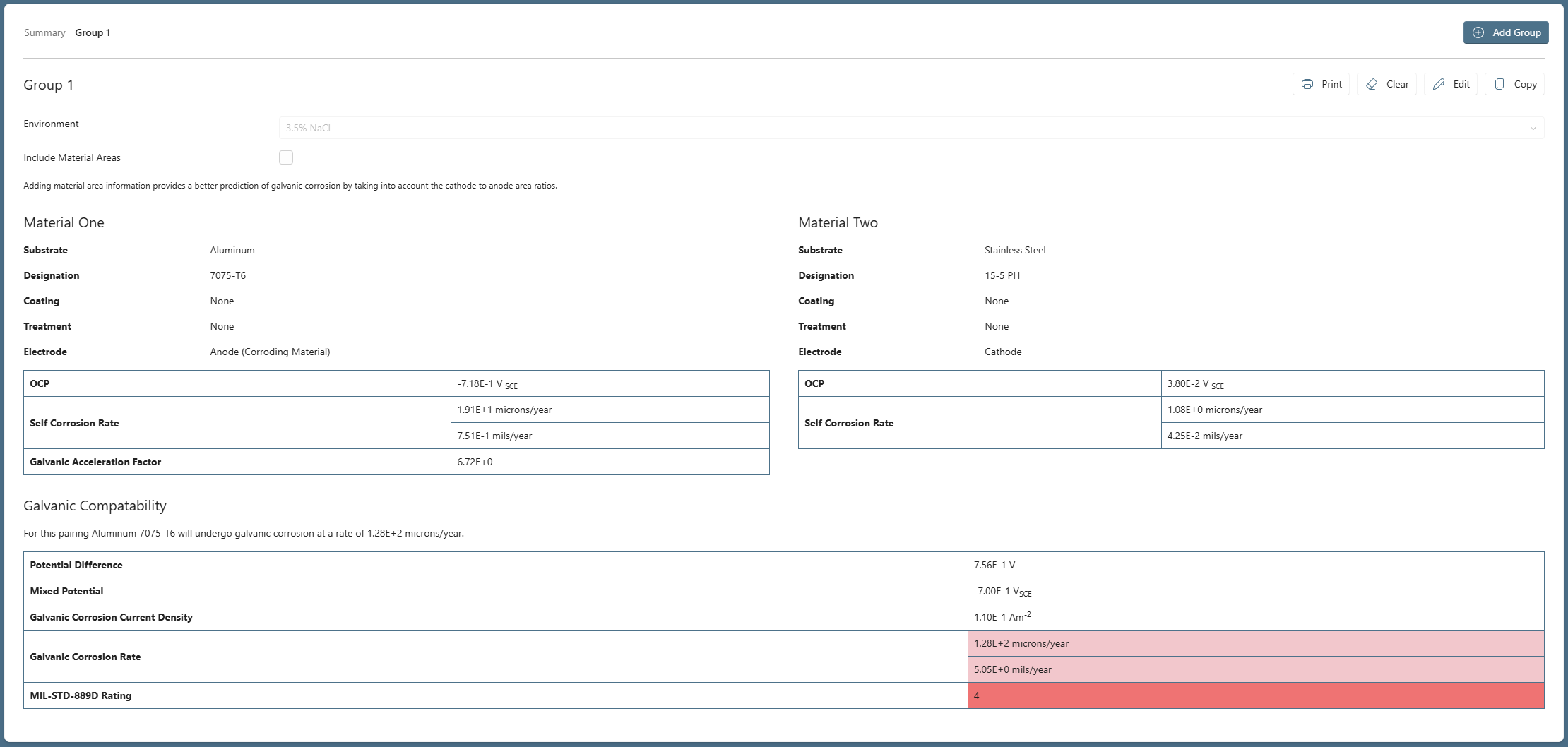